BIRLA CARBON BLOG
INSIDER KNOWLEDGE FOR ALL THINGS CARBON BLACK
Achieving High Electrical Resistivity in Rubber Compounds
Reading Time: 3.25 minutes
Introduction
One often associates carbon black with electrical conductivity, and the presence of carbon black in rubber insulating compounds has been regarded as detrimental in this aspect. But what if we need carbon black performance properties but also high electrical resistivity? Perhaps we need to rethink the conventional reasoning, since it has been proven that the addition of certain types of carbon blacks in rubber goods has limited impact on electrical insulation. This is extremely important in certain rubber applications where the benefits of carbon black are required without the disadvantages of higher conductivity.
The Challenges and Importance of Highly Resistive Rubber Products
Carbon black is frequently added to elastomers to improve mechanical properties and wear resistance. At the same time, the electrical resistivity of such a composite is usually reduced, which is highly undesirable for insulative applications. Therefore, rubber manufacturers are challenged to control electrical resistivity while also meeting all the targeted performance properties.
Uses are growing for rubber components with high levels of electrical resistivity in applications that can also benefit from the reinforcing nature of carbon black. High resistivity rubber compounds have also gained favor in the automotive industry, in large due to the need for weight reduction in electric vehicles. Extruded rubber goods, such as weatherstripping which seals between dissimilar alloys in the vehicles – such as steels and lightweight aluminum – can cause galvanic corrosion problems unless the rubber is sufficiently resistive. Consequently, the auto industry is beginning to require resistivity values from 106 to 109 Ω·cm for insulating rubber goods.
Such high levels of rubber resistivity can be achieved by adding “white” fillers such as calcium carbonate, clays, or precipitated silica. But in these cases, the weight of the component can increase and the level of processability, surface finish, and mechanical properties are severely compromised.
The Solution: Birla Carbon BC1004 and BC1083
Birla Carbon offers two solutions, BC1004 and BC1083, to rubber manufacturers facing these high resistivity requirements. Both are high quality carbon black products with medium structure and low surface area which allow compounders to produce highly loaded, electrically resistive rubber compounds with a reduced cost and excellent processing (fewer screen pack changes and higher throughput). They also feature low residue content for a Class A extruded finish.
- Birla Carbon BC1004 is suitable for applications requiring clean carbons for excellent surface finish and durability as well as for use in dense and blown weatherstrip for a matte finish and high resistivity.
- Birla Carbon BC1083 is applicable in class A profiles, coolant-, fuel-, non-automotive hoses, timing belts, vibration isolators, O-rings, and gaskets. It provides even higher resistivity levels than
Modern rubber formulations containing Birla Carbon’s BC1004 and BC1083 offer significantly higher electrical resistivity than traditional ASTM N550 type products (Figure 1, left). These Birla Carbon products can be used as the sole filler or in conjunction with white fillers to ensure the rubber article is highly resistive and maintains both aesthetic appeal and physical properties, such as tensile strength (Figure 1, right).
Figure 1 Volume resistivity and tensile strength of Birla Carbon BC1004 and BC1083 reinforced rubber* compared to standard ASTM grades. Representative automotive specification limits are indicated by dashed lines.
*Rubber formulation: 100 phr EPDM, 80 phr carbon black, 55 phr white filler, 60 phr oil,19.5 phr co-agents and sulfur cure system.
Conclusions
A major market has developed for high resistivity rubbers in the automotive industry. This represents a challenge to compounders who must balance processability, cost and performance properties with high electrical resistivity. Standard carbon blacks significantly reduce electrical resistivity at practical concentrations prohibiting use in these applications.
Birla Carbon’s BC1004 and BC1083 allow compounders to produce high resistivity products versus conventional ASTM carbon black grades without affecting processability or performance. These products allow the development of high resistivity, cost effective formulations with good extrusion properties, targeted resistivity, and lighter weight compounds than predominantly white filled compounds. Birla Carbon has expertise in design and application of these and other carbon blacks and is eager to collaborate with customers to optimize their products.
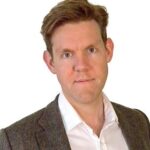
Dr. Lewis Tunnicliffe is a lead scientist in the Birla Carbon rubber product development group. His work involves developing new types of carbon blacks and synergistic materials for enhancing rubber compound performance for the tire and rubber goods industries. Dr. Tunnicliffe joined Birla Carbon in 2016 and holds a Ph.D. in materials science (rubber materials) from Queen Mary University of London. He is interested in viscoelasticity properties and the fatigue and fracture of rubber materials.
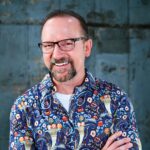
Stephen Crossley is a senior scientist on the Birla Carbon rubber product development group. His work involves coordinating quality and technical service support as well as support for other business growth opportunities like Continua™ and new product developments. Stephen joined Birla Carbon in 2000, and he has over 25 years of experience in rubber compounding and development. His interests include providing customer solutions, mentorship, and project management.
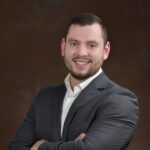
James Kollar is a senior research associate in the Birla Carbon rubber product development group. His work includes developing and evaluating new carbon blacks and synergistic materials for rubber applications. James joined Birla Carbon in 2018 and hold a master’s degree in chemistry. He is interested in reinforcing material networks and network formation mechanisms within polymer systems.
WANT TO LEARN MORE ABOUT CARBON BLACK AND THE PROPERTIES THAT MAKE IT IDEAL FOR YOUR PLASTICS, COATINGS, AND INKS APPLICATIONS?
Leave A Comment