BIRLA CARBON BLOG
INSIDER KNOWLEDGE FOR ALL THINGS CARBON BLACK
The Roles of Carbon Black in Wire & Cable Conductor, Insulation and Jacketing Applications
08 / 02 / 2021 by Jinil Kim, Dr. Natalie Harris, Dr. Jun Tian
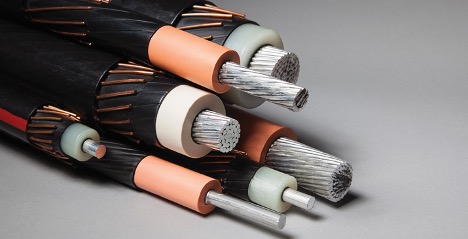
Reading Time: 6 minutes
Conductive plastic compounds have a variety of applications including conductor and insulation shield for wire and cables, antistatic, electrostatic dissipation (ESD), electromagnetic interference (EMI) shield, and metal replacement. Plastics are typically electric insulators. It is common to use a conductive additive to tailor the conductivity of plastics to a particular application. In comparison with carbon nanotubes, carbon fiber, graphene, and metal flake or wire, carbon black is the most cost-effective additive to make conductive compounds. This is due to carbon black’s highly engineered process technology and easy dispersibility.
This blog talks about the key properties of carbon black and how they are related to conductivity performance, especially as it relates to wire and cable applications.
1. Conductivity of Carbon Black
In conductive plastic applications, carbon black is mainly used to increase the conductivity of plastic materials or to dissipate electricity to protect against static electrical discharge. The conductivity of these plastics is determined by the type and loading of the carbon black as well as the compounding and manufacturing processes for finished parts. The plastic resin type and additives also influence the conductivity, but for this discussion let’s focus specifically on carbon black. Carbon black consists of primary nanoparticles fused to form aggregates which are three-dimensional chain-like structures. Measured properties of carbon black such as surface area, structure, porosity, and surface activity all play a role in the conductive performance of plastic material as summarized in Table 1. Conductive blacks tend to have a higher surface area, higher structure, higher porosity, but lower surface activity, i.e., higher chemical cleanliness. In addition, the loading and the dispersibility of carbon black also impact the conductivity (Table 2).
Table 1. Carbon Black Fundamental Properties & Conductivity
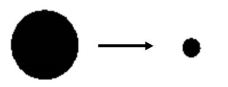
Surface area (Primary particle size)
- High surface area (smaller primary particle size) carbon blacks provide more specific surface area for electron transfer.
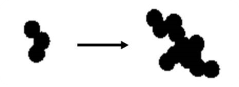
Structure (Aggregate size)
- Higher aggregate size leads to the formation of the conductive path at lower loading.
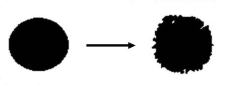
Porosity
- Carbon black with high porosity contains a higher number of aggregates per unit weight.
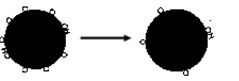
Surface Activity
- Lower surface activity (higher chemical cleanliness) shows higher intrinsic conductivity that helps the formation of a conductive path.
Table 2. Effect of Carbon Black Loading and Dispersion on Conductivity
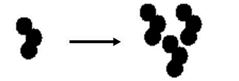
Carbon black loading
- Higher Carbon black loading leads to the formation of a conductive path.
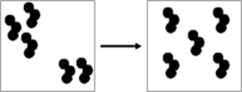
Dispersion
- Better dispersed carbon black reduces the distance between the carbon blacks and leads to the formation of a conductive path.
2. Wire & Cable Applications
Wire & Cable industries consume the largest amount of conductive carbon black, the majority of which is used in the conductor and insulation shields of medium and high voltage cables. Figure 1 illustrates the typical structure of the power cables. The conductor shield may bond with the metal conductor to provide a smooth interface and a homogeneously distributed electric field to the insulation. The insulation shield protects the insulation from corona damage and provides safety. Carbon black in the conductor and insulation shields play a critical role in the long-term service life of the cable.
Depending on the specific application and the type of carbon black, the carbon black loading may vary from ~22% to ~44% by weight. Although not a conductive need, carbon black is also used in the cable jacket to reinforce UV protection.
3. Requirements of Carbon Blacks in Wire & Cable Applications
Carbon black is an essential component used in both the conductor and insulation shields to impart the desired conductivity performance. To choose a carbon black, we can look at desired carbon black loading. The decision is then whether to use a carbon black delivering higher conductivity at lower loading or a carbon black with the lower conductivity at higher loading. However, the carbon black selection depends not only on the required conductivity specification but also on the other requirements including dispersibility, rheology, mechanical performance, and surface smoothness.
As mentioned earlier, the conductivity of carbon black compounds is determined not only by the type and the loading of carbon black, but also by the process conditions including compounding and final cable extrusion. A full understanding of all these aspects ensures optimization of the conductive performance.
3. 1 Dispersibility
Carbon blacks show higher levels of dispersibility with decreasing surface area, lower porosity, and higher structure. As shown in the property-performance relationship in Table 1, with the exception of structure, there is an obvious trade-off between ease of dispersion and delivering high levels of conductivity.
Therefore, when higher conductivity carbon black is required, it is important to find a balance between dispersibility and conductivity. Carbon blacks with differing levels of dispersion are shown in Figure 3.
We can look at a couple of scenarios:
Scenario 1:
Higher surface area and medium structure carbon black: Here sufficient dispersion energy has to allow full de-agglomeration to the individual aggregates to deliver the optimal conductive performance and other secondary attributes.
Scenario 2:
Lower surface area and high structure: With this balance of properties the carbon black is highly dispersible and will yield conductive performance but at slightly higher loadings compared to the carbon black described in Scenario 1. This means lower dispersion energy is sufficient to provide good dispersion for the desired conductivity performance. It is worth mentioning that overly aggressive mixing or too much energy input with this type of carbon black can lead to the breakdown of the aggregate (higher structure = more friable aggregate) and hence, deliver lower than the desired performance.
3.2 Cleanliness
For wire and cable applications, the cleanliness of a carbon black is as important as the conductivity and dispersibility. Higher cleanliness improves dispersion, conductivity, surface smoothness, and reduces screen pack changes in the compounding process.
Birla Carbon’s Ultra technology ensures excellent physical cleanliness; more specifically, low levels of impurities as measured via sieve residue and ash tests.
On the other hand, due to product quality and chemical regulations, chemical cleanliness is also an important requirement. The chemical cleanliness of carbon black can be measured with sulfur, PAH, ionic, and other chemical composition analysis methods.
In addition to the physical and chemical cleanliness, the moisture level present in carbon black also needs to be controlled or minimized prior to compounding as excess moisture adversely affects the dispersion, the conductivity and the surface finish.
The demand of conductive plastics for wire and cable is increasing, and our carbon blacks play a significant role. Birla Carbon is one of the leading carbon black manufacturers and can offer extensive expertise in the wire and cable application arena. We are responding to the various demands of the market with a full portfolio of carbon black products. Our technical experts across the globe stand ready to collaborate with our customers to help them succeed by discovering the right solutions to any application challenges. There are many options when it comes to choosing and using carbon black, so we encourage you to contact a Birla Carbon technical expert to maximize your chances of success.
Additional Blogs for reference
Ensure Your Compound Comes Out Right: Seven Common Mistakes to Avoid
Jinil Kim
Jinil is currently Senior Manager of the Specialty Blacks application laboratory in South Korea and Technical Service, North Asia, for the plastics, inks and coatings markets. He has been working in the coatings industry since 1998 and joined Birla Carbon in 2009. He likes to communicate with customers and enjoys developing solutions to customers’ application problems. He also hopes to support the use of carbon black in a variety of applications. Jinil completed his doctoral course in electrochemistry from the Korea Polytechnic University. He received his Master of Science in industrial chemistry in Inha University and his Bachelor of Science in chemical engineering from Korea Polytechnic University.
Dr. Natalie K. Harris
Dr. Natalie K. Harris began her career with Birla Carbon in 1990 at the European R&D Center in Bristol, UK, with responsibilities for the Materials Analysis Group. Dr. Harris relocated to the USA in 1998 with the role of Director, Applications Technology laboratory at the Corporate Headquarters in Marietta, Georgia, with the responsibility for managing programs for carbon black evaluations in tire, MRG, plastics, inks and coatings. A few years later, Dr. Harris moved out of the laboratory environment to lead a global role in developing new products for the inks and coatings markets. Dr. Harris’s current role is Technical Service Manager, North America, for the plastics, inks, and coatings markets.
Dr. Jun Tian
Dr. Tian has been working in the plastics industry since graduating from the University of Connecticut in 2004, and has been with Birla Carbon for 8 years. Dr. Tian currently serves as Principal Scientist to lead a technology team and collaborate with our customers to develop solutions to a variety of challenges for applications of specialty blacks.
WANT TO LEARN MORE ABOUT CARBON BLACK AND THE PROPERTIES THAT MAKE IT IDEAL FOR YOUR PLASTICS, COATINGS, AND INKS APPLICATIONS?
Leave A Comment