BIRLA CARBON BLOG
INSIDER KNOWLEDGE FOR ALL THINGS CARBON BLACK
Carbon Black and High Jetness Engineered Plastics – Three Parameters to Consider
04 / 02 / 2021 by Dr. Natalie K. Harris
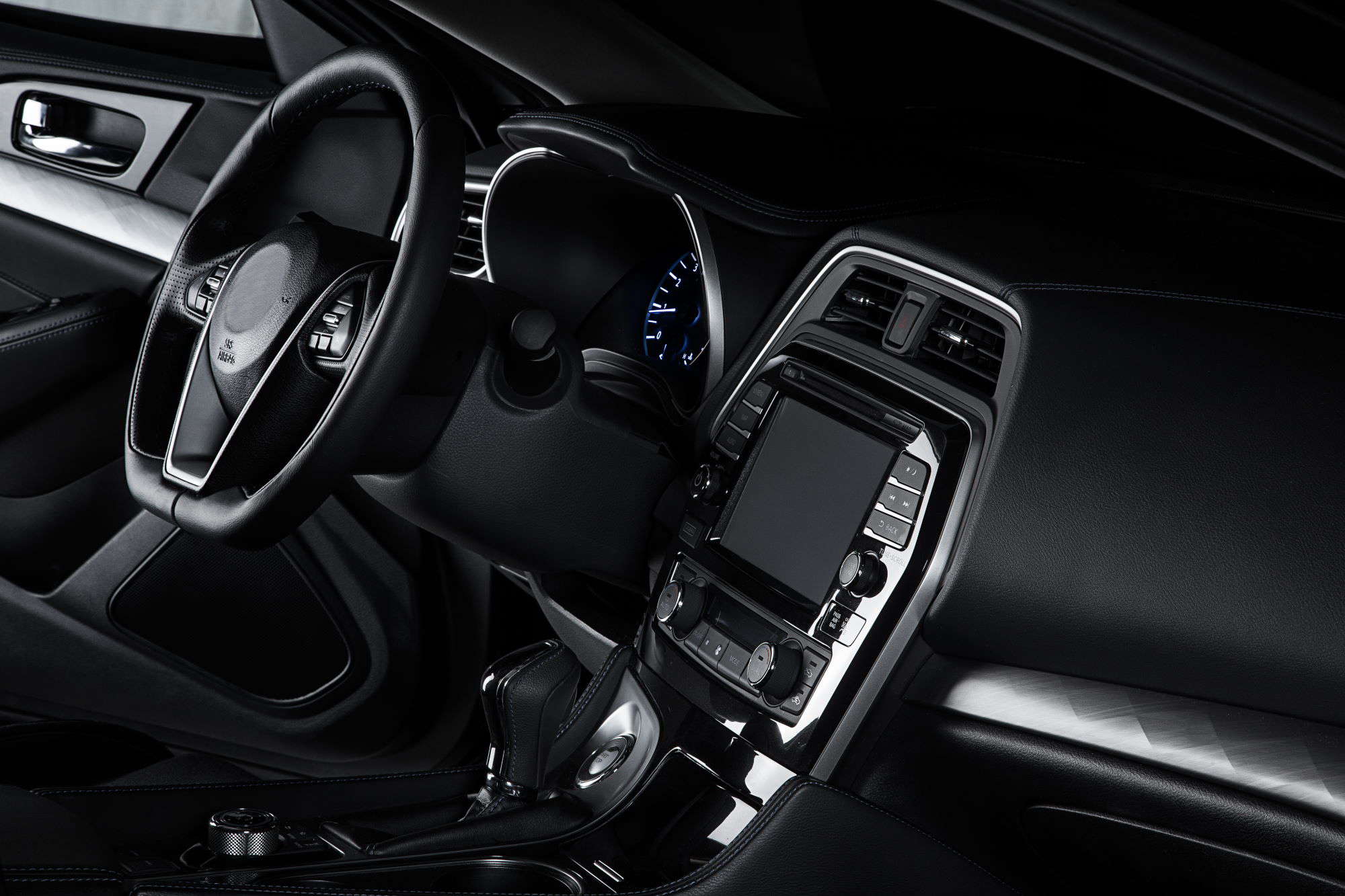
Reading Time: 3.25 minutes
End use applications for engineered plastics include automotive interior and exterior, household appliances, and consumer electronics. Market forecasts show an annual demand increase of over 4% for these plastics systems in the next few years. These applications frequently feature a jet black appearance as a key selling feature. Specially engineered carbon blacks can deliver the high level of blackness targeted in many engineering plastics applications. These carbon blacks can also give an excellent balance of jetness and blue tone to meet market needs.
Let’s look at the parameters you should consider to realize the full performance benefits with these very special carbon black pigments.
Parameter #1 – Pigment Selection
Carbon black needs to have a high surface area to deliver high jetness in end-use applications. Jetness increases with increasing carbon black surface area. This high surface area can only be fully utilized when a good level of carbon black dispersion is achieved.
So what do we mean by good level of dispersion? This can be defined at both the macro- and micro-dispersion levels. Macro-dispersion is visible to the naked eye and very important for surface finish aesthetics. However, for color performance a good level of micro-dispersion is needed. For a given carbon black, morphology in a specific resin/polymer matrix, improving levels of carbon black micro-dispersion result in higher levels of blackness. A carbon black needs to be fully dispersed at the micro-level, both distributively and dispersively. This means FULL deagglomeration to the aggregate level. Aggregates are the primary units of carbon black. You can see agglomerates and aggregates in the accompanying micrograph.
Masterbatch compounding is a proven method for improving the dispersion of carbon black and reaching the desired color performance. This is in addition to proper resin selection and optimal carbon black loading. Generally speaking, higher carbon black loadings will increase the masterbatch viscosity and the carbon black agglomerates will experience more shear. Specialty additives compatible with the carbon black may be leveraged to promote wettability and enhance dispersion.
Parameter #3 – Dispersion Process
The high surface area of carbon blacks targeted for high jetness make achievement of good dispersion extremely challenging. There are various inputs to the mixing process that need to be optimized including screw speed, throughput, and equipment type/design. Carbon black dispersion increases with screw speed but decreases with higher throughput. Types of equipment used vary. Twin screw extruders allow a great deal of flexibility through the unique screw configuration and modular design. For highly loaded masterbatch systems, Farrell Continuous Mixers (FCM) are efficient and provide good quality masterbatch materials.
Measuring Dispersion
The industry is very familiar with the use of blown film to assess macro-dispersion and light microscopy. Assessing micro-dispersion, however, is not quite as straightforward via electron microscopy. Fortunately, we can use color as an indirect measure. When developing a mixing protocol or new formulation, we can characterize dispersion by measuring jetness, blue tone, and gloss of injection molded parts. Tint strength is also a good indicator of the hiding power that the pigment is delivering under a given set of processing conditions.
So what can Birla Carbon pigments deliver?
Birla Carbon has a family of pigments designed for high jetness applications in engineering plastics. The graph shows typical color performance of Birla Carbon’s Raven 2000 series and a newly developed ultra-high jetness pigment Raven 5100 Ultra. With increasing surface area, the accompanying improvement in jetness (as measured by decreased Hunter L) is seen. Similar trends are seen in a variety of resin systems including SAN, PP, PC, PA, ABS and PP.
For further information, please contact Birla Carbon’s technical team.
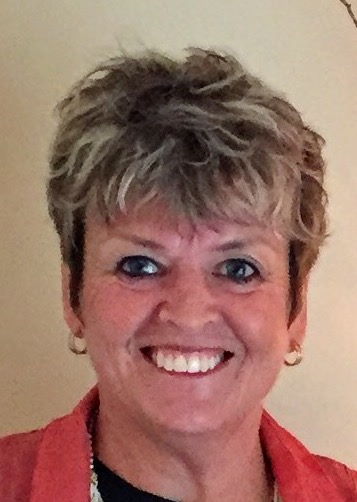
Dr. Natalie K. Harris
Dr. Natalie K. Harris began her career with Birla Carbon in 1990 at the European R&D Center in Bristol, UK, with responsibilities for the Materials Analysis Group. Dr. Harris relocated to the USA in 1998 with the role of Director, Applications Technology laboratory at the Corporate Headquarters in Marietta, Georgia, with the responsibility for managing programs for carbon black evaluations in tire, MRG, plastics, inks and coatings. A few years later, Dr. Harris moved out of the laboratory environment to lead a global role in developing new products for the inks and coatings markets. Dr. Harris’s current role is Technical Service Manager, North America, for the plastics, inks, and coatings markets..
WANT TO LEARN MORE ABOUT CARBON BLACK AND THE PROPERTIES THAT MAKE IT IDEAL FOR YOUR PLASTICS, COATINGS, AND INKS APPLICATIONS?
Leave A Comment