BIRLA CARBON BLOG
INSIDER KNOWLEDGE FOR ALL THINGS CARBON BLACK
Carbon Black’s Influence on Cut and Chip Resistance in Tire Treads
Reading Time: 3 minutes
Introduction to Tread Durability
In-service wear of tire tread is a leading cause for replacing tires and can be a safety issue. Broadly speaking, wear of the tread can be broken into two categories:
- Abrasive / thermo-oxidative wear. This wear is characterized by the gradual removal of the tread due to common frictional forces experienced in driving combined with normal environmental exposure. This form of wear would be the most familiar to everyday commuters.
- Cut and chip wear. This type of wear is common in off-the-road applications. Sharp, large protrusions from the road surface can cut the tread surface. The cut pieces can then be torn away as a large chip with continued use of the tire.
Tires needing the most cut and chip resistance are those that are operating in severe environments. For example, giant earth-moving tires 15-20 feet in diameter, massive combine tires running through sharp agricultural stalks, or the more familiar tires of a dump truck running over sharp debris.
How Carbon Black Impacts Cut and Chip Resistance
The cut and chip wear phenomena are complex and quite different from normal over-the-road wear. The challenge is to understand and optimize the parameters that contribute. From the perspective of carbon black, there are three levers typically used to increase the cut and chip resistance of a rubber compound: surface area, structure, and surface activity.
Surface Area: High fineness grades provide more surface area with which the rubber molecules can bond. This results in high energy dissipation, creating a barrier for a crack tip, or tear, to continue growing.
Surface Activity: This refers to the level of volatile oxygen groups at the surface of the carbon black. A carbon black with a lower surface activity, or a more ‘dead’ surface, allows for rubber molecules to move more freely and slide across the carbon black surface, creating friction. This friction is also a source of energy dissipation, and retards crack or tear growth.
Structure: Lower structure grades greatly increase intrinsic tear strength. The exact mechanism behind this phenomenon is less understood than those for surface area and activity. One explanation is that the lower structure grades have less rubber trapped in the filler aggregates and allow the compound to stretch more before breaking. This is a means of optimizing ‘toughness’.
The Rubber Compound Balancing Act
Practically speaking, compounding for cut and chip will also include balancing other properties. For example, soft compounds are very susceptible to abrasive wear – so perhaps the solution for an agricultural tire primarily used in soft soil is much different than a dump truck which is required to drive along cement roads.
One must also consider the ever pressing need to reduce emissions for environmental sustainability. As noted above, the main mechanism for increasing tear resistance is to increase energy dissipation. High energy dissipation is directly correlated to high rolling resistance and lower fuel efficiency. High energy dissipation is also correlated to heat build-up in the tire, which has secondary effects on wear resistance.
Birla Carbon’s Offerings
Birla Carbon offers several specialized products which are targeted at increasing tire durability. BC2041 and BC2285 are exclusive Birla Carbon, carbon blacks specially designed to provide significant improvements in cut and chip resistance along with improvements in tear strength when compared to standard products like N134 and N115. For further information on our products or further discussion regarding the durability of your tread compounds, reach out to our technical team on our contact page.
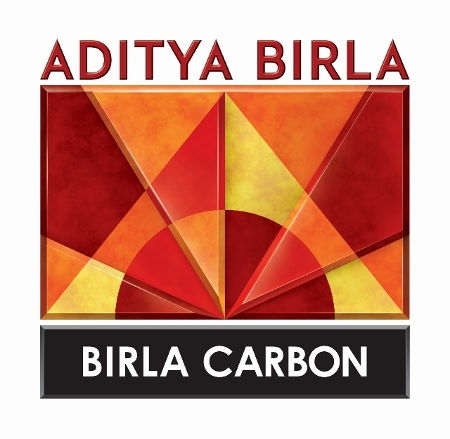
Seth Young – Technical Svc Manager at Birla Carbon
WANT TO LEARN MORE ABOUT CARBON BLACK AND THE PROPERTIES THAT MAKE IT IDEAL FOR YOUR PLASTICS, COATINGS, AND INKS APPLICATIONS?
Leave A Comment