BIRLA CARBON BLOG
INSIDER KNOWLEDGE FOR ALL THINGS CARBON BLACK
Conductive carbon additives, a readily available opportunity to improve lithium-ion cell manufacturing and performance
Reading Time: 5.5 minutes
When people think about lithium-ion batteries, they think about how these devices deliver electricity. Certainly, the materials used to power them are inherently electrically conductive, right? As it turns out, it is nowhere near as much as you might expect. Energy-storing materials need a bit of a boost to deliver the electricity needed to power our devices.
Imagine lithium-ion cells as a bucket, where water is energy (watts). NMC811 is large, and old faithful LFP is smaller. Importantly, the opening of the bucket is largest on LFP and relatively small on the NMC811 cell. There is more water in the NMC811 bucket (since it is large), but the opening is the biggest on the LFP (despite holding less water) – which one would be used in a race to move water? The energy in a cell behaves in a similar way to the water in the bucket. To dump all the energy out of the cell, a suitable opening is needed. Similarly, to refill the energy in my cell, easy access to filling the bucket is needed. Conductive additives such as carbon black or carbon nanotubes facilitate access to energy by aiding the electron pathways in materials that are relatively poor at accepting charge. What about the buckets? Carbon additives adjust the opening on these buckets, trading access for capacity. In the case of an electric car, these differences are like having a more responsive throttle or the ability to charge faster.
Carbon additives are typically one of the lowest cost contributors to the bill of materials for a lithium-ion cell. Yet, they are critical to achieving a high-performance design and contribute directly to the characteristics of a cell. To give a sense of the scale and the size of the material, a typical carbon black conductive additive is imaged below against a scale of 0.5 μm. The particles are very small. Consider that cathode active materials (CAM) and anode active materials (AAM) are on average (d50) around 10 to 20μm, so orders of magnitude higher.
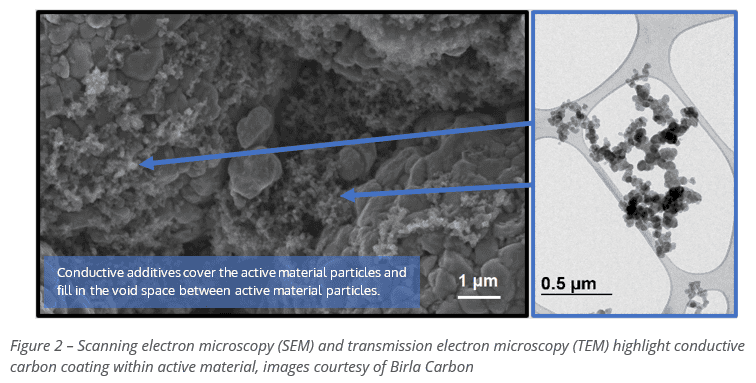
Furthermore, the carbon particles link together to create a branched structure. This structure is specifically designed to fill the interstitial space (free space) between cathode/anode materials, allowing electrons to zoom around at will on these super-speed highways. In poor designs, these highways become extremely tortuous (bendy) and narrow (slow). The cell would take all day long to charge and forever to squeeze out what energy it has.
Is there an ideal amount of conductive additive? Because of the variability of interstitial space and conductivity of a given CAM/AAM batch, there is a certain amount of variability in particle size. Determining the optimal conductive carbon loading involves some trial and error and, eventually, trial and success. Cell designers know roughly the right amount, but until it is trialed in a proposed cell design, it can be expected to see significant changes in performance based on the conductive carbon content. At Birla Carbon, our scientists and engineers regularly run loading studies to determine the optimal conductive carbon loading for a given active material. Cells that have too little conductive carbon fail to perform, even at low current rates. The optimal amount of conductive carbon, typically less than 10 wt%, can deliver above an 80% capacity retention at very high current rates. (Brief technical aside: C-Rate is the speed (current) at which a cell’s total energy can be discharged/charged. A 1C current rate is the current at which a battery is charged or discharged in 1 hour. 2C is complete charge or discharge in half an hour, 0.5 C. is 2 hours, and so on. Just remember, cell capacities differ, so it is very much cell specific.)
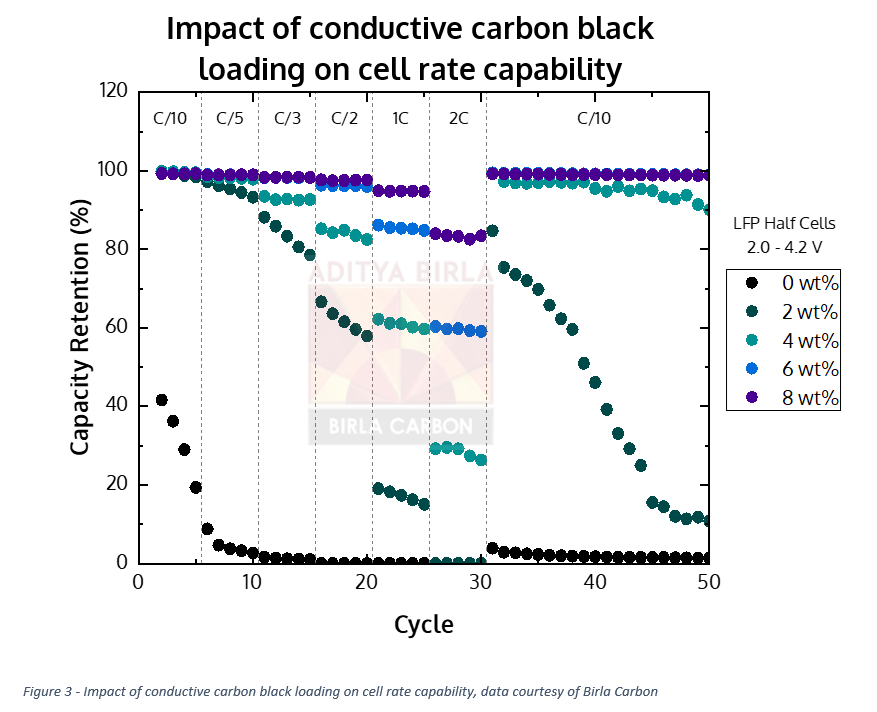
The chart indicates that for this LFP cell, increasing amounts of conductive additive support a greater level of capacity retention at higher rates. As such, one could be inclined to add as much conductive carbon as possible. However, the intrinsic energy capacity (‘bucket size’) of these carbon additives is very small, far lower than that of the CAM/AAM they are mixed with. This means that there is ultimately a trade-off between cell capacity (bucket size) and rate capability (opening size), with an optimum to be found depending on the end application needs.
One of the primary goals of the battery industry is to increase the energy density of cells. Can conductive carbons play a role in making this happen? Yes! Birla Carbon is actively investigating next-generation conductive carbons, like carbon nanotubes (CNTs). Loading at 20-30% of the weight of a traditional carbon additives, CNTs allow battery manufacturers to increase the amount of active material in their formulations, which increases the battery’s energy density and, therefore, electric vehicle driving ranges. Returning to the bucket analogy, CNTs are like having many more tiny holes in the bucket lid to carry the water out/fill it back up.
One of the biggest challenges with CNTs is that they are difficult to mix into battery formulations. To get the most out of your conductive additives, they must be able to coat the surface of your CAM/AAM and fill in the interstitial space between these particles. CNTs, though, tend to clump together, causing a processing nightmare for researchers at lab scale and process engineers at the gigafactory scale alike. Fortunately, Birla Carbon can provide a carbon black/CNT composite hybrid material that negates these processing issues, using the carbon black to improve dispersion and using the CNTs to deliver the high conductivity needed to push the limits on the energy density of lithium-ion batteries.
Thank you for taking the time to read this short wrap-up of the current state of the art for conductive additives. Despite making up such a small component of lithium-ion batteries, conductive additives can be truly transformative to the overall performance.
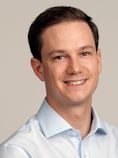
Nicholas Dunkley
Nicholas Dunkley is Head of Market Development for the Energy Systems team at Birla Carbon. His focus is on business development for graphite anode active materials and conductive additives for battery markets. He has 15 years experience working on automotive applications and its supply chain. Post-graduation, his career began in the design of automotive catalyst systems, where his research became a reality with millions of cars on the road using his designs. In 2017, he pivoted to work with cathode materials (LFP & high nickel) for the lithium-ion market. Nicholas received his bachelor’s degree in mechanical engineering from Surrey University.
WANT TO LEARN MORE ABOUT CARBON BLACK AND THE PROPERTIES THAT MAKE IT IDEAL FOR YOUR PLASTICS, COATINGS, AND INKS APPLICATIONS?
Leave A Comment