BIRLA CARBON BLOG
INSIDER KNOWLEDGE FOR ALL THINGS CARBON BLACK
Engineering Plastics–Three Ways to Get That Perfect Jetness
7 / 16 / 2018 by Paul Hoffman
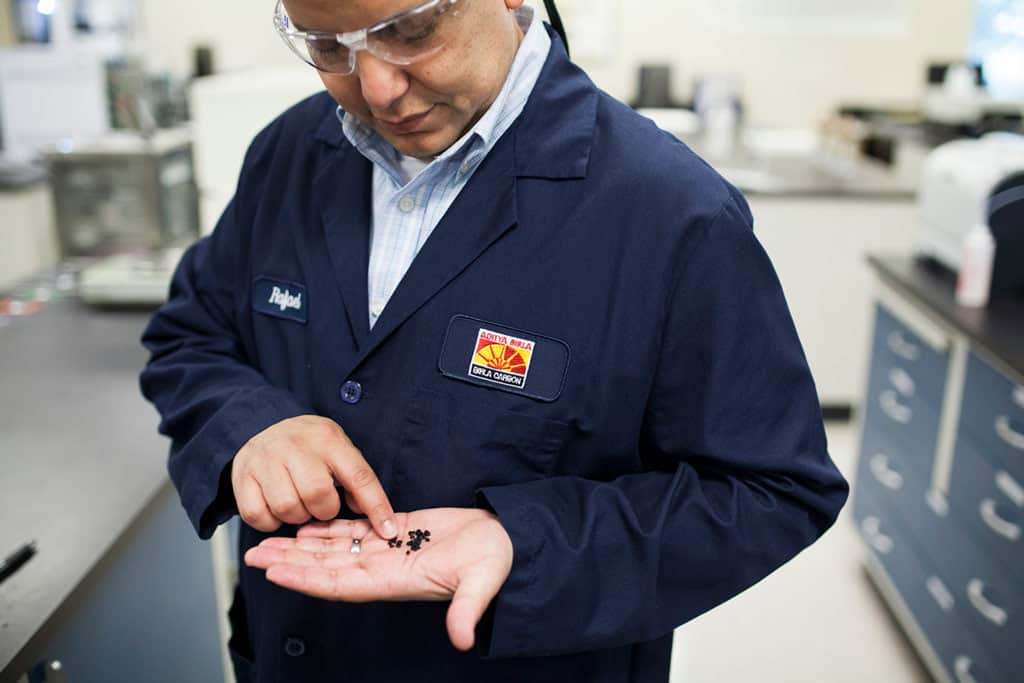
Reading Time: 3.25 minutes
Most engineering plastics applications need a certain level of jetness. But that ideal level of jetness depends on a few interrelated factors, all of which are important for getting the jetness just right. If you keep all of these factors in mind, you should have no problems maximizing your mix’s retention of mechanical properties — and hitting your overall color targets — in the most cost-effective manner possible.
Assuming your mixing process is already defined and the jetness target is fixed, here are three helpful hints to achieve the perfect jetness:
1. Keep your surface area low
The higher the surface area of the carbon black, the lower the loading of carbon black you’ll need in order to meet your jetness target. In short, higher surface area leads to higher jetness. But keep in mind that carbon black affects opacity as well as your mix’s mechanical properties, such as viscosity. As surface area increases, dispersion becomes more difficult throughout the mixing system.
Additionally, within the range of carbon blacks typically used for high jetness engineering plastics, higher surface area usually equates to higher-cost carbon black. For all these reasons, it’s a smart idea to keep the loading of carbon black to the minimum necessary to achieve the jetness you’re aiming for.
2. Choose the right carbon black for your system
As the surface area of carbon black increases, an increasing amount of mixing energy is necessary to disperse the carbon black effectively. If dispersion is not complete, micro-scale carbon black agglomerates will start to act as inclusions, which will cause the mechanical properties of your mix to suffer. Plus, these agglomerates will also result in pips on the final part surface, ruining an otherwise glossy, high-jet appearance.
The most effective way to achieve even dispersion is the masterbatch route: Use a twin-screw mixer and then dilute the mix to the final loading in the compound. If you don’t have access to this level of high-energy mixing, another option is to choose a different carbon black with a more highly branched aggregate structure. In carbon black terminology, structure is measured as oil adsorption number, or OAN, with a higher number indicating higher structure.
On the other hand, if you’re using direct compounding as your defined mixing system, you’ll typically end up with a lower-viscosity system than if you’d used masterbatch. In that case, the most reliable way to achieve good dispersion is to choose a higher-structure carbon black than you’d use in a masterbatch system.
3. Keep your carbon black clean
No matter how precisely you choose and measure your carbon black, your surface’s mechanical properties and finish can turn out poorly if your carbon black has high levels of physical impurities. A certain amount of impurities are unavoidable in all carbon blacks, but these are normally so small they’re measured as parts per million (ppm) residue. To minimize the risk of physical impurities in your carbon black, choose a product with a residue below 20 ppm.
Depending on the specific application, you may also want to keep a close eye on the cleanliness of your carbon black, which can also be a critical factor. For example, quite a few regulations define carbon black requirements for food and skin contact applications. If your application has one of these requirements, you should make sure to choose a carbon black whose purity has been designed accordingly. And if you’re ever unsure about the carbon black requirements for your application, make sure you consult with a carbon black product stewardship manager before you buy.
You have many choices when it comes to carbon black, so save time and maximize your chance of success by keeping these key points in mind. Or better yet, consult with an applications expert from Birla Carbon to come up with the best solution for your project needs.
PAUL HOFFMAN
Paul currently heads the global marketing and product management activities for Birla Carbon Specialty Blacks Business. He joined Birla Carbon in 1995 and has held positions in process development, product development, business development and marketing. Paul received his MBA from the Georgia Institute of Technology, his MS in Materials Science and Engineering from the University of California, Davis and his BS in Mechanical Engineering from Tennessee Technological University.
WANT TO LEARN MORE ABOUT CARBON BLACK AND THE PROPERTIES THAT MAKE IT IDEAL FOR YOUR PLASTICS, COATINGS, AND INKS APPLICATIONS?
Leave A Comment