BIRLA CARBON BLOG
INSIDER KNOWLEDGE FOR ALL THINGS CARBON BLACK
Five (Less Obvious) Reasons Your Coatings Formulation Is Not Performing
5 / 21 / 2018 by Dr. Richard Abbott
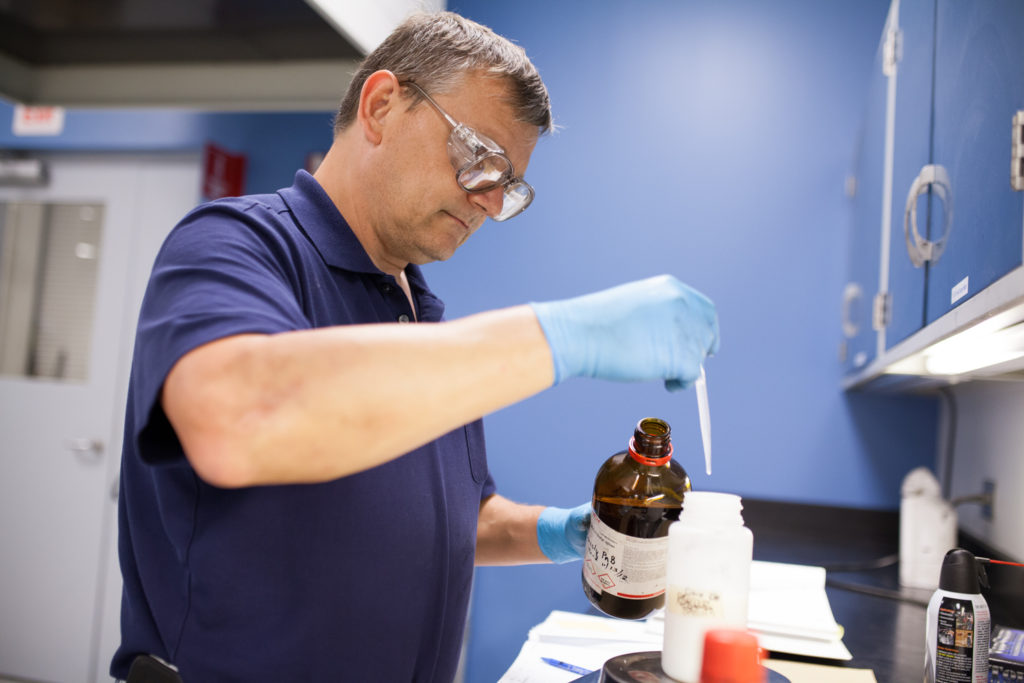
Reading Time: 3 minutes
It’s crucial to choose the right carbon black to meet your needs — whether that’s color, conductivity, or both. But if you’re not seeing optimal performance in your coatings formulations, carbon black itself may not be the root problem. The issue may lie with some other ingredient, an unexpected interaction, or an incorrect application.
Here are five not-so-obvious reasons your carbon black may not be performing optimally, along with my tips for how to address each of them.
1. Pigment loading
It sounds simple: the more pigment you add to your system, the more opacity and coverage you get. In truth, though, the equation is a little more complex. That’s because carbon black increases not only your mix’s opacity but also its viscosity. When you load your system with solid particles, it’s entirely possible to overload it, creating a system in which the pigment volume concentration (PVC) increases beyond the critical level. The key indicator of this is low glossiness in the final application. We recently worked with a customer who encountered exactly this problem, and it turned out he had added too much pigment to the mix. The high surface area of the carbon black had adsorbed too much resin and left the system resin lean.
2. Solvent flash speed
The temperature and dryness of your work environment can significantly impact the speed at which solvent flashes off your coating. Obviously you need to flash the solvent off at some stage, but if you let it flash off too quickly, you may see premature surface curing, resulting in a brittle surface. You’ll know this is happening when you notice a bit of condensation (or “sweating”) and hazing on your coating. When you’re working outdoors, especially in areas with wild temperature swings, this can become a major issue. So to be safe, my advice is to err on the side of flashing more slowly, even though this may increase your cure times a little.
3. Solvent polarity
Tweaking the solvent flash speed (replacing isopropanol with isobutanol, for example) can lead to small subtle shifts in the solvent polarity. These shifts can affect the film formation and gloss. Be careful not to chase your tail around this loop.
4. Resins
All commercial resins show some natural variations in manufacturing. Even resins derived from natural feedstocks can be affected by subtle variations in their makeup and the refining process. This variation — coupled with the natural variation in other ingredients, as well as your curing process — can interact to knock you out of tolerance of your coating in surprisingly dramatic ways. These interactions can be particularly difficult to diagnose.
5. Dispersants
A good dispersion is crucial for uniform tone and functionality. But with literally hundreds of dispersants to choose from, how can you be sure you’re using the right one for your current system? Carbon black’s low bulk density and few surface function groups make it particularly tricky to wet, which means its agglomerates must be broken down by a specialized dispersant in order to achieve ideal dispersion. Because this is an in-depth topic, we’ll be revisiting it in an upcoming blog post.
Keep in mind that the cause of your formulation’s performance issue may not be just one of these factors, but an interplay among several. Double-check the weights of your ingredients and your temperature. Then eliminate each cause one by one.
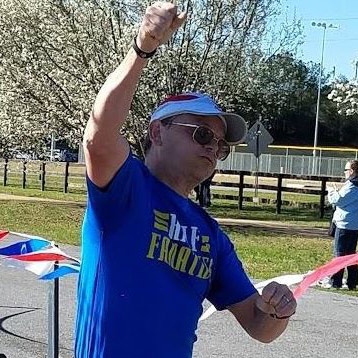
Dr. Richard Abbott
Dr. Richard Abbott has been with Birla Carbon for 16 years. He began his career at the European Central Lab (ECL) as an inks and coatings scientist before moving to the Marietta technical lab where he has spent the majority of his time furthering the liquid segments. He greatly enjoys the variety of work he is able to do and relishes the opportunity to tackle the next unique application or formulation.
WANT TO LEARN MORE ABOUT CARBON BLACK AND THE PROPERTIES THAT MAKE IT IDEAL FOR YOUR PLASTICS, COATINGS, AND INKS APPLICATIONS?
Leave A Comment