BIRLA CARBON BLOG
INSIDER KNOWLEDGE FOR ALL THINGS CARBON BLACK
Maximizing the Fatigue Performance of Rubber Components
05 / 10 / 2021 by Dr. Lewis Tunnicliffe
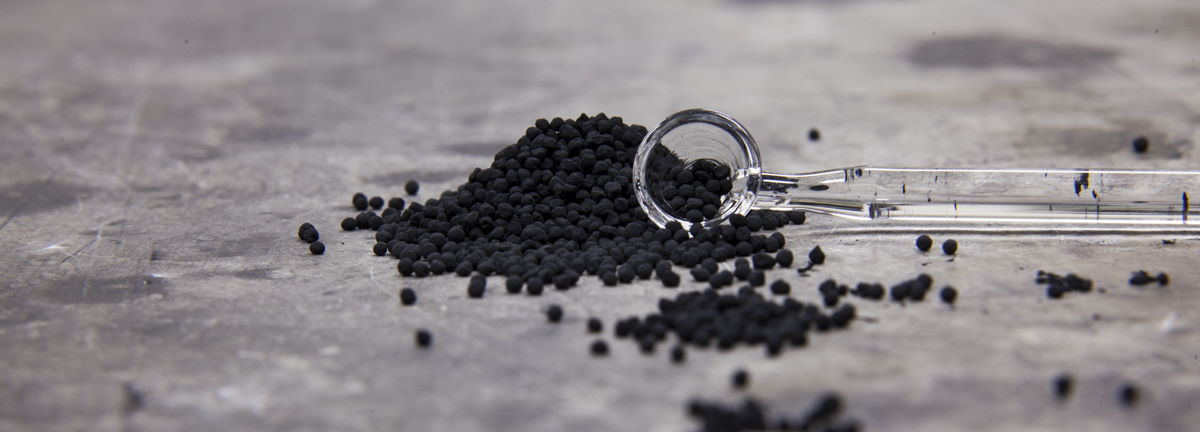
Reading Time: 5 minutes
Across a vast range of industries, rubber components play safety critical roles in activities every single day. As such, rubber components need to be durable and long lasting. While there are many ways in which a rubber component can fail in service, mechanical fatigue is probably the most common failure mechanism which affects nearly all rubber-based components. In future blogs, we will explore solutions to other failure mechanisms such as abrasive wear and cut-chip, chemical attack and swelling and inelastic failures.
With mechanical fatigue, we are concerned with the long-term performance and lifetime of rubber components, subjected to repeated mechanical loading and unloading cycles. Conveyor, timing and transmission belts, various tire components, AV mounts and vehicle tracks, are all examples of components which undergo repeated mechanical cycling during operation.
Mechanical fatigue of rubber starts with the initiation of cracks from local in-homogeneities (crack precursors) within the rubber compound. This, then proceeds over progressive loading cycles via the incremental growth of cracks through the body of the rubber, up to the point of catastrophic failure. Based on this failure mechanism, we will need to consider both, the nucleation of cracks, i.e. the homogeneity of the compound and the intrinsic fatigue crack growth resistance of the compound.
Compound developers are often challenged with extending the fatigue lifetime of their compounds without sacrificing other aspects of performance. Conversely, developers will seek to improve other aspects of compound performance, such as dynamic performance without sacrificing the component’s lifetime. Fortunately, we have a rich and well-developed scientific framework to tackle such challenges as well as some basic materials selection guidelines to help us.
Mode of Control of Deformation
First off, we need to understand the cyclic operational conditions of the component. Is the deformation of the rubber controlled by the application of a cyclic load or the imposition of a defined cyclic displacement? This is critical since it allows us to tailor the compound stiffness in such a way that we minimize the stored energy during deflections which is available to grow cracks. For example, under a deflection-controlled condition, we could target a softer compound to minimize the energy stored in the compound under deflection and suppress the crack growth. The reverse is true with load control where we could target a stiffer compound to minimize component deflection.
Selection of Rubber
Selection of the rubber for the application is one of the most important compounding decisions affecting mechanical fatigue performance. Natural rubber is a great option for crack and tear resistant compounds. Its ability to crystalize under application of strain, leads to a self-reinforcement just ahead of crack tips. This mechanism arrests and blunts the cracks during cyclic relaxing and non-relaxing deformations. Of course, not every application is amenable to use of natural rubber. Applications at very high temperatures or in chemically harsh conditions may necessitate the use of specific synthetic rubbers. Most synthetic rubbers do not demonstrate the remarkable strain crystallizing behavior of natural rubber. Instead, they rely entirely on particulate reinforcement to achieve the required crack growth and tear resistance.
Selection of Reinforcement Agents
Reinforcing agents such as carbon blacks, play a key role in determining the crack growth and tear resistance of rubber components. Selection of the right formulation loading level, surface area and structure level of the carbon black is critical. Further improvements are made by choosing a carbon black that can achieve a good dispersion during the compound mixing process and also has minimal physical impurities. The same is true for other particulate co-agents in the formulation. Undispersed filler agglomerates and raw material impurities lead to an increase in crack precursor size and number in a compound, both of which have a deleterious effect on fatigue life.
In natural rubber, carbon black reduces the onset displacement levels required for strain crystallization to occur by amplifying the local strains in the rubber matrix. This essentially catalyzes the self-reinforcing capability of natural rubber. Carbon black also introduces additional energy dissipation mechanisms into rubber compounds and this is one of the key reasons why we see increases in tear strength and crack growth resistance in filled versus unfilled rubber. More external work needs to be applied to fracture a filled rubber in order to compensate for the energy dissipated by carbon black in the viscoelastic process zone ahead of the crack tip. This is especially critical for non-crystallizing rubbers.
We need to be careful here because too much energy dissipation can lead to detrimental heat buildup in components under cyclic loading conditions and can compromise dynamic mechanical performance (e.g. rolling resistance). As is always the case with rubber technology, a careful balance is required.
Characterizing Mechanical Fatigue
In reality, very few rubber components fail in ways that are completely consistent with the rapid, inexpensive and ubiquitous rubber lab tests, common in our industry. Relatively simple testing like tensile fracture or tearing does not provide us with the complete picture we require to fully understand and engineer the fatigue performance of rubber compounds. Fortunately, at Birla Carbon, we are exceptionally well equipped with state-of-the-art facilities to investigate and characterize mechanical fatigue mechanisms and link these back to practical rubber compounding. These facilities include high throughput fracture mechanics-based fatigue crack growth equipment, fatigue life/crack nucleation testing and our world-class microcopy facilities.
Please reach out to us to see how we can help you improve your compound and components’ mechanical fatigue performance. By leveraging Birla Carbon’s unique carbon black portfolio and our extensive technical capabilities, together with your compound and design expertise, we can work to reduce trade-offs between dynamic performance and durability, across a wide range of applications. In addition, check out some of our latest work and collaborations on these topics at the linked papers which are open access and free to download (https://www.mdpi.com/2073-4360/12/1/203).
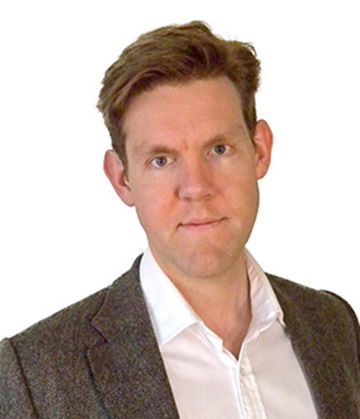
Dr. Lewis Tunnicliffe
Dr. Lewis Tunnicliffe is a lead scientist in the Birla Carbon rubber product development group. His work involves developing new types of carbon blacks and synergistic materials for enhancing rubber compound performance for the tire and rubber goods industries. Dr. Tunnicliffe joined Birla Carbon in 2016 and holds a Ph.D. in materials science (rubber materials) from Queen Mary University of London. He is interested in viscoelasticity properties and the fatigue and fracture of rubber materials.
WANT TO LEARN MORE ABOUT CARBON BLACK AND THE PROPERTIES THAT MAKE IT IDEAL FOR YOUR PLASTICS, COATINGS, AND INKS APPLICATIONS?
Leave A Comment