BIRLA CARBON BLOG
INSIDER KNOWLEDGE FOR ALL THINGS CARBON BLACK
The Evolution of Anti-Vibration Systems in Automotive Applications – Part 1
Reading Time: 4.0 minutes
The automotive industry has undergone significant technological advancements in recent years, with a shift towards more efficient, environmentally friendly vehicles. One key aspect of this evolution lies in the development of anti-vibration systems (AVS) which play a crucial role in improving the overall driving experience. These systems rely on the properties of elastomer composites to provide effective vibration isolation and overall noise, vibration, and harshness (NVH) reduction.
Part 1 of this article delves into the evolution of AVS in automotive applications by examining the various types of elastomeric components and their applications. Part 2 will focus on the challenges posed by the transition to electric vehicles.
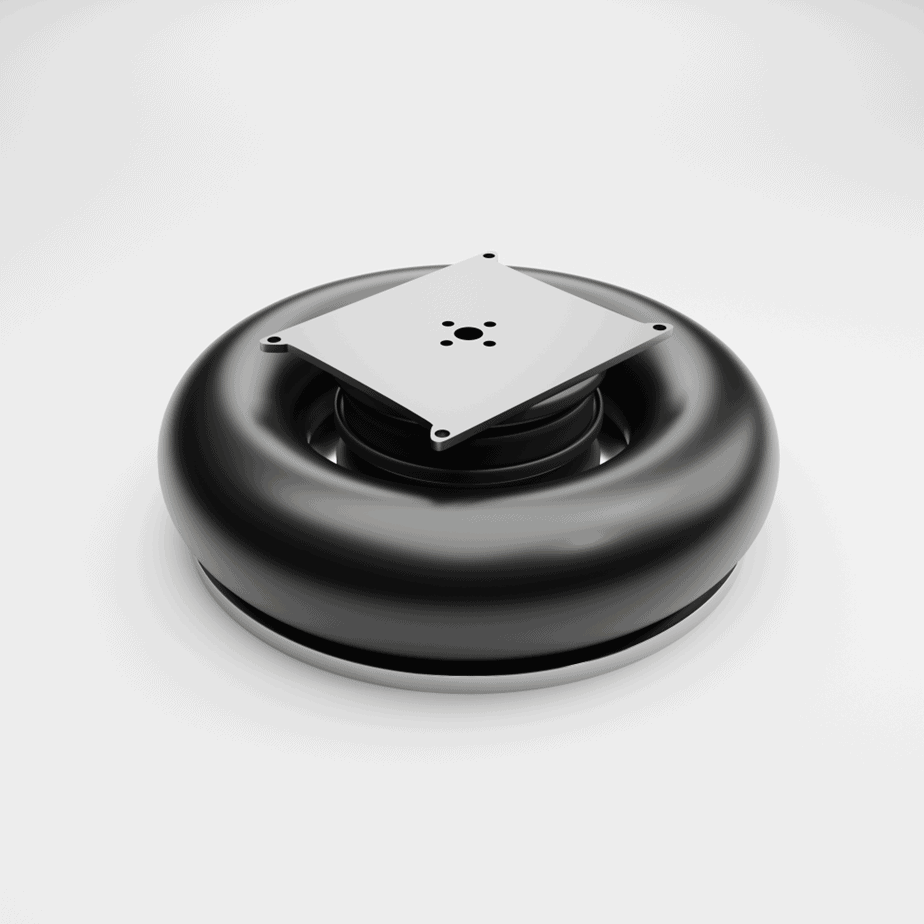
The Role of Elastomers in AVS
Elastomers are widely used in the automotive industry due to their unique combination of properties, such as flexibility, durability, and resistance to heat and chemicals. In AVS, elastomers act as the primary damping and isolation elements, providing both spring rate and damping characteristics to control vibrations. The effectiveness of elastomers in AVS is due to their ability to absorb and dissipate energy, reducing the transmission of vibrations and noise to the vehicle and its occupants.
Spring Rate and Damping Characteristics
The spring rate of a composite is related to its dynamic stiffness, while its damping characteristics are determined by its hysteresis (energy loss). Elastomers and elastomer composites can be engineered to have a specific spring rate and damping properties, allowing manufacturers to tailor the performance of the AVS to suit a particular vehicle or application by material selection. For instance, carbon black selection can play a crucial role in compound design for AVS. Using a carbon black with a low surface area and medium-low structure such should yield a compound with very low spring rate and moderate damping. This can be compared to a carbon black like BC2295, which has a higher surface area but still with low structure, which maintains most of the low spring rate but would improve damping.
Heat Resistance and Durability
Durability is a key requirement for elastomers used in AVS as they must maintain their performance and properties over the vehicle’s lifespan. Material selection is again a large component of designing a part that meets application requirements, in this case durability. Durability is one of the reasons natural rubber is a favorite in compound design for AVS. The durability of natural rubber can be augmented with appropriate carbon black choice. Returning to the above comparison of BC1083 and BC2295, the latter will offer superior durability due to its higher surface area and resulting higher tensile strength compared to BC1083. Durability is also enhanced by choosing a carbon black with a high level of physical cleanliness so as to avoid inclusions that could act as crack initiators, such as choosing BC1031 over an ASTM N550.
Another important property of elastomers in automotive applications is their resistance to heat. As vehicles operate in a wide range of temperatures and conditions, it is crucial that the elastomeric components can withstand these extremes without degradation. For internal combustion engines ( ICEs), there has been continual trends of switching from mostly natural rubber to more temperature resistant polymers such as BR, NBR… but this can add significant costs to the compounds.
Applications of Elastomers in AVS
Elastomers are used in various components within an AVS, each serving a specific purpose in reducing vibrations and improving the overall NVH performance.
Engine System
Elastomeric engine mounts are designed to absorb vibrations from the engine and isolate them from the vehicle’s chassis, thereby reducing noise and vibrations felt by the driver and passengers. These components operate at high frequencies but generally low amplitudes so they must provide excellent damping and isolation performance while also being resistant to heat and chemicals found in the engine environment, especially in the case of ICEs. Engine mounts tend toward softer compounds and are often filled with low surface area and low structure carbon blacks such as BC1083.
Suspension System
In the suspension system, elastomeric components such as bushings are used to isolate larger vibrations from the road and improve ride comfort. These are especially important in instances like potholes, which have low frequency but high amplitude. They must provide both stiffness and damping properties to ensure stable handling and a comfortable driving experience. Due to the large amplitude of these occurrences, strength and durability are crucial to consider. BC2295 offers impressive damping improvement as well as improved durability compared to a standard carbon black like N330.
Body System
Elastomeric components are also used in the body system, primarily in the form of mounts and isolators between the vehicle’s body and chassis. These components help to reduce the transmission of vibrations from the engine, suspension, and road to the vehicle’s interior, improving overall NVH performance.
Exhaust System
The exhaust system is another area where elastomers are employed, specifically in the form of hangers and mounts that support the exhaust components. These elements must provide both vibration isolation and heat resistance, as exhaust systems can reach high temperatures during operation.
Conclusion
The use of elastomers in AVS automotive applications continues to evolve as the technological demands steadily increase around energy efficiency, performance, and comfort. As the automotive industry continues to transition towards electric vehicles, the role of elastomers in AVS will become even more critical, with new challenges to overcome and opportunities to innovate. In Part 2 of this article will examine the specific challenges in AVS for electric vehicles and the integration of elastomeric components in electric vehicle architectures.
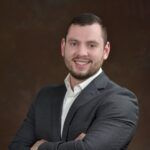
James Kollar
James Kollar is a scientist in the Birla Carbon rubber product development group. His work includes developing and evaluating new carbon blacks and synergistic materials for rubber applications. James joined Birla Carbon in 2018 and holds a master’s degree in chemistry. He is interested in reinforcing material networks and network formation mechanisms within polymer systems.
WANT TO LEARN MORE ABOUT CARBON BLACK AND THE PROPERTIES THAT MAKE IT IDEAL FOR YOUR PLASTICS, COATINGS, AND INKS APPLICATIONS?
Leave A Comment