BIRLA CARBON BLOG
INSIDER KNOWLEDGE FOR ALL THINGS CARBON BLACK
Formulating Carbon Black in Adhesives & Sealants
07 / 01 / 2021 by Dr Reuben Correia
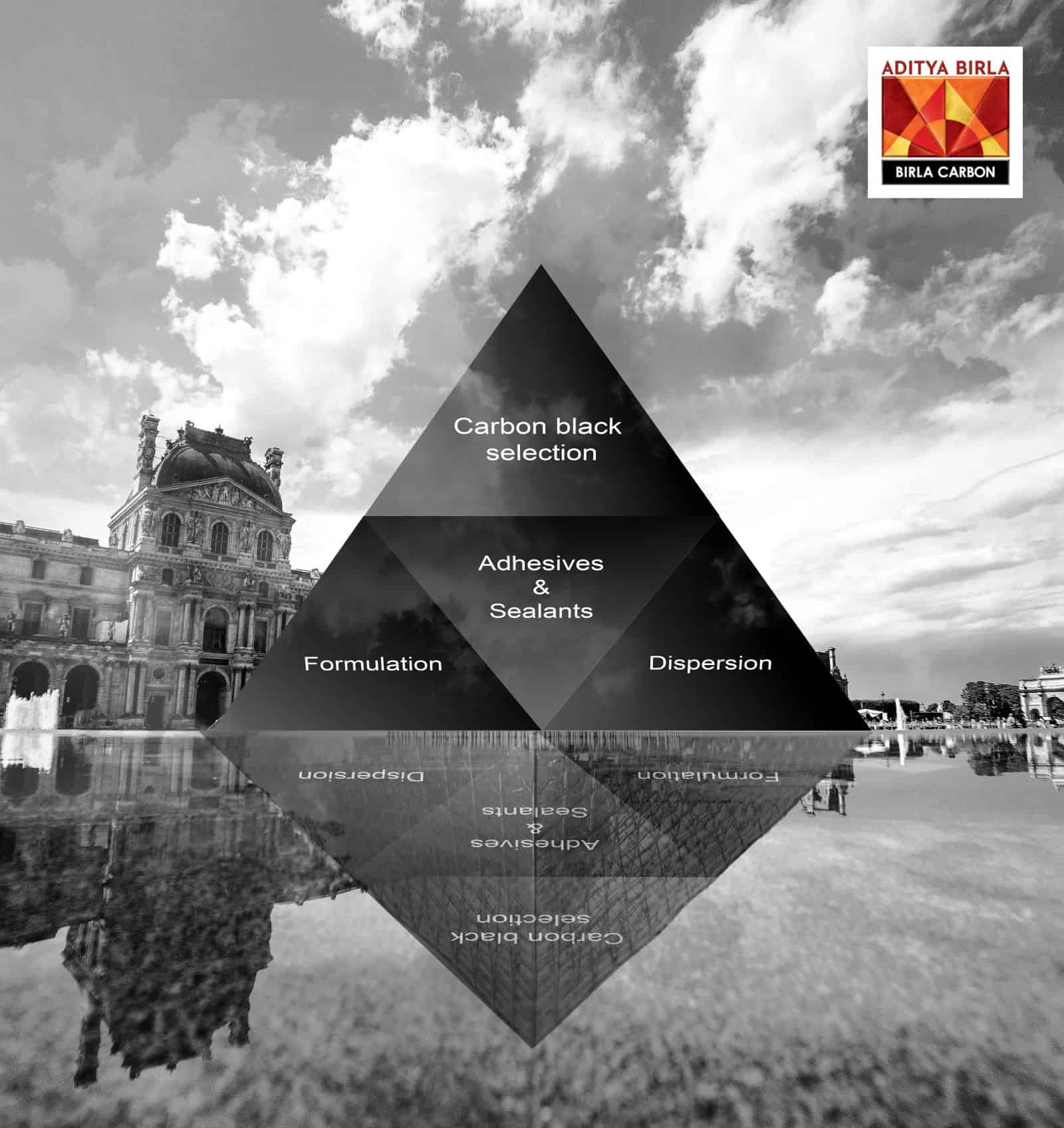
Reading Time: 4.25 minutes
Carbon black is typically a key ingredient in Adhesives & Sealants in all chemistries spanning PolyUrethanes, Acrylics, Epoxies, PolySulfides, Butyls, Silicones and Hybrids. When qualifying a new carbon black in a new product or as a potential offset, it is critical to understand the Performance Triangle by looking at carbon black selection, formulation and dispersion.
Carbon Black Selection
Knowing the role of the carbon black will help in the selection process. When carbon black is used primarily as a black colored pigment, it can be used at roughly 2% by weight of the formulation. To increase the jetness of a product at the same loading of carbon black, an entirely new carbon black with higher surface area might be needed. Where additional performance properties are necessary which may include UV and thermal conductivity, increased tensile strength and elongation, control of rheology and viscosity, faster green strength, improved adhesion, and in some cases carbon dioxide absorption, carbon black is typically used at over 10% by weight of the formulation.
Formulating with Carbon Black
Several formulators treat carbon black as an inert solid and when used as a pigment at 2% of the formulation, this usually does not create any issues. However, when carbon black is used at over 10% of the formulation, new product development or qualifying a potential offset can often times be challenging or even frustrating. This is mainly due to the fact that no two separately sourced carbon blacks are identical, even though they may look the same on paper as far as colloidal properties are concerned. Hence, the formulator needs to be patient in understanding the performance of the new carbon black and ideally see some advantages with usually minor tweaking of the process or formulation.
In only a few instances, formulators may see an incompatibility of the new carbon black in their formulation. This is either seen right away or after heat aging for a few days. When this happens, formulators are usually anxious to change the carbon black to eliminate the incompatibility instead of understanding why this is happening. It is valuable for both you and the supplier to understand why there is this incompatibility. This information could lead towards a beneficial, permanent solution. When necessary, we also offer Ultra clean carbon black products which can minimize or eliminate incompatibility between carbon black and your formulation.
Carbon Black Dispersion Explained
If you are trying to increase jetness of the formulation at the same loading of carbon black, you may try a new carbon black with higher surface area, but it is critical to understand if both are compared using the same dispersion process. If the dispersion process is the same, it is possible that the carbon black with higher surface area performs the same or underperforms on jetness even though macro-dispersion i.e. appearance / grain or Hegman grind is identical. If this occurs, ultimate micro-dispersion with the higher surface area carbon black has not yet been achieved i.e. all the higher surface area carbon black agglomerates are not completely broken up into their aggregates throughout the matrix of the polymer system. This is either due to insufficient residence time provided with the same amount of shear, or higher shear needed for the new carbon black.
High shear equipment like a twin-screw extruder with a relatively fixed residence time of shear is usually not the right piece of equipment for evaluating the performance of a variety of different carbon blacks in lab evaluations even if macro-dispersion in all formulations are identical. Also, when comparing carbon blacks in the lab using high shear batch mixers, one has to be careful about not using disperser blade(s) since although high shear, they are great for low viscosity i.e. coating or paint formulations but create a vortex i.e. just mixing air around the blade(s) when used for higher viscosity sealant formulations. Ideally, these blades should be replaced with butterfly blades that work great in breaking the carbon black agglomerates into well dispersed aggregates throughout the formulation. Alternatively, if one has a double planetary mixer, this works great as well in this regard as long as sufficient residence time is provided.
Finally, if purchasing a new batch mixer for sealant production, focus on optimal height to diameter ratio that is specific to your needs and the most efficient cooling capability since some polymers are more sensitive to higher temperatures than others, typically attained during processing. Alternatively, if purchasing a new twin-screw extruder for sealant production, focus on the right balance in variety of extruder elements to provide more shear and residence time than needed for current formulations in planning for future more demanding formulations.
When you are looking for a new carbon black to meet your new product requirements or just looking for an alternate source of carbon black, come speak to Birla Carbon where our experts have decades of experience in Adhesives & Sealants and carbon black and we have a wide range of high performance products providing complete solutions.
Dr. Reuben Correia
Dr. Reuben Correia is New Product Development Manager, Adhesives & Inks at Birla Carbon and is based at the state-of-the-art Birla Carbon Technology Center in Marietta, Georgia. He leads product innovation in adhesives and inks using Stage-Gate process. Dr. Correia has about two decades of experience formulating Adhesives and Sealants. He has developed Best-In-Class global products that have enabled customers achieve primerless adhesion to a wide variety of metal, painted, plastic, and glass substrates, fast adhesion development even at low temperatures, and quick cure. He also has expertise in efficient manufacturing of sealants using continuous twin screw extruders and a variety of batch mixers. Prior to his current role, Dr. Correia has held positions of Technology Management, Senior Chemist, and Six Sigma Black Belt at GE Silicones and Momentive. He received his Ph.D in Synthetic Organic Methodology and Mechanistic Chemistry from the University of Maryland, College Park in 2003.
WANT TO LEARN MORE ABOUT CARBON BLACK AND THE PROPERTIES THAT MAKE IT IDEAL FOR YOUR PLASTICS, COATINGS, AND INKS APPLICATIONS?
Leave A Comment