BIRLA CARBON BLOG
INSIDER KNOWLEDGE FOR ALL THINGS CARBON BLACK
Low Migration Inks for Sensitive Packaging – Birla Carbon Specialty Blacks
04 / 19 / 2021 by Chinmoy Dhole
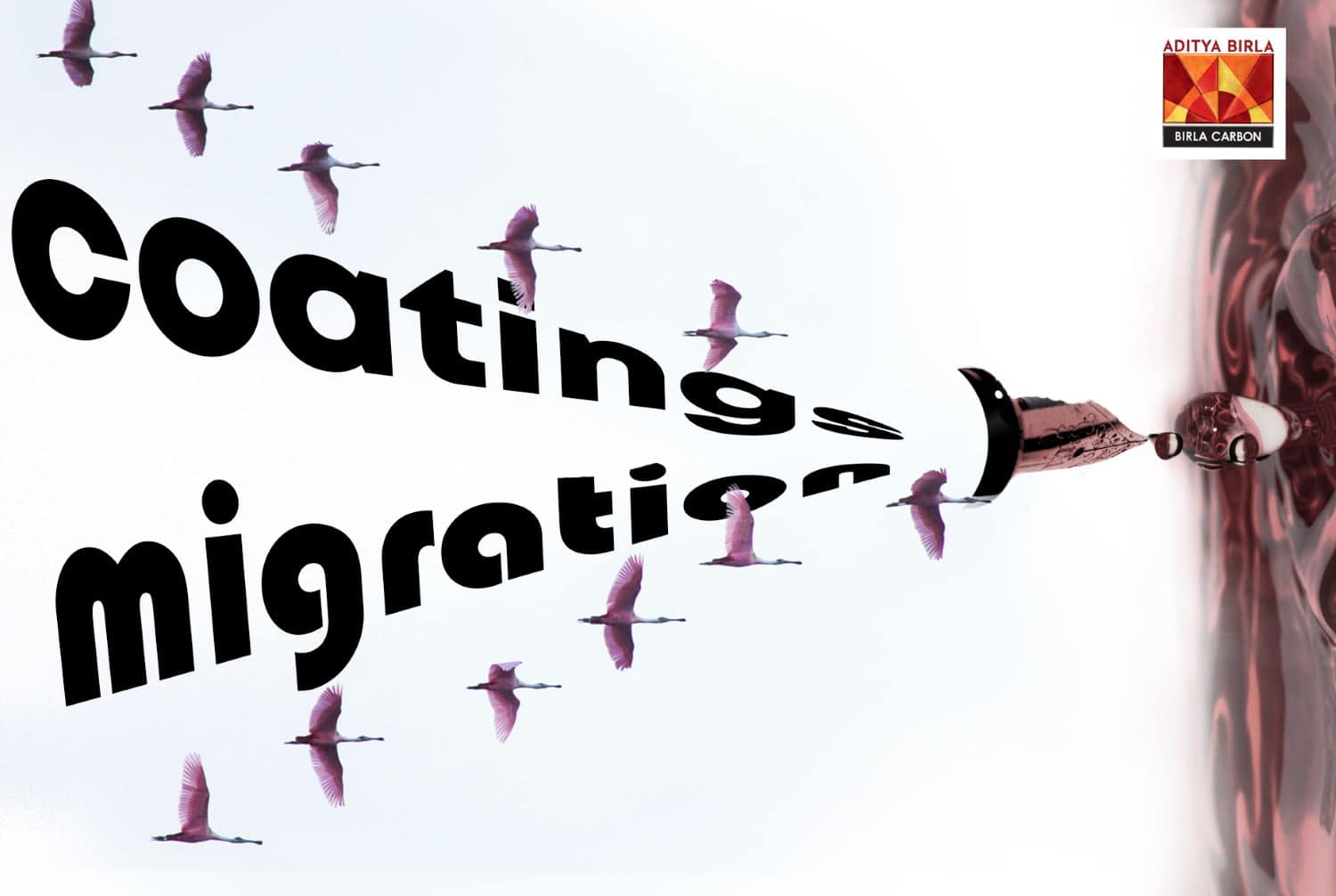
Reading Time: 5.25 minutes
Migration in Packaging due to Inks
The same ink that creates attractive packaging with gorgeous designs can also soak through and then potentially make the inside food unsafe. >97% of all foodstuffs sold on the American and European markets are packaged. Over the last few years, the share of direct packaging (with no inner bag) has increased. In this type of packaging, the food comes into direct contact with the unprinted inner side of the packaging material. So, it is important to understand what ink migration is, what causes it, and what options are there to minimize or prevent it in packaging.
How ink migration occurs
Migration takes place when ink components penetrate from the printed to the unprinted (product facing) side of the packaging substrate. It also can result from wet-ink printing, set-off, or incompletely dried ink on the top side of the sheet contacting the bottom of the sheet above it in a stack or a roll.
Because of their chemical characteristics and molecular sizes, some substances (migrants) can migrate from the printed side through the substrate onto the unprinted side. This highly depends also on the barrier properties of the substrate.
Evaporation and condensation may trigger migration in packs in which foods can be boiled or microwaved. Heat-sterilizing a package may do the same harm.
The substances transferred from packaging to the food inside may not always be detected in organoleptic testing (odour and taste) or when consumed, but can be identified by chemical analysis.
Low Migration (LM) Inks – major application areas
The term “low migration” packaging is commonly used to designate materials used in the whole packaging structure whose chemicals will not migrate from the packaging into the inside packed product. To qualify as low migration packaging, these materials contained in the packaging structure, including inks, must not have any migratory chemicals which would affect the appearance, flavour, taste, odour or the safety of the product inside.
Labels and packages for foods and beverages, napkins, placemats and other printed items that have direct or indirect contact with food are the most important applications for LM inks. Cosmetics and pharmaceutical packaging also have high demand for LM Inks. Tobacco packaging is categorized as the other key application area. Traces of contaminants can affect the performance of electronic items, thereby packaging of these products may also need the protection of low migration inks.
Migration is time-dependent
The longer the potentially migrating components are next to the packaged foodstuff, the greater the risk of migration. There are many additional factors that affect the rate or extent of migration including:
- type of packaged foodstuff
- temperature at which the packaged product is stored and storage time
- nature of the packaging itself
- process used to cure the ink
If slow evaporating solvents are used for improved printability of solvent-based and water-based inks, care must be taken with these choices as slow evaporating solvents have a high potential to be retained in the printed product and could subsequently migrate to the packaged food. The rate of migration of volatile and migrant components increases two-fold for each 10 deg C temperature rise.
Regulatory Framework
Food packaging inks are formulated and made considering many varying parameters related to the substrate, application and end-use. In general, these inks are formulated and made in accordance with the EuPIA Good Manufacturing Practices (GMP).
The other most influential regulation for ink migration is “Swiss Ordinance” – to identify components deemed safe to use in inks for packages containing food and other sensitive products. The ordinance also sets “acceptable” migratory limits (in ppb) for these components. Nestlé and other leading brands have made it the basis of their own stringent requirements for packaging safety.
In the U.S., the FDA regulates ink components that may come into direct or indirect contact with food, but it does not certify inks as “low migration” or “food safe.” Food packaging compliant inks are tested under standardized migration test conditions to prove that under these conditions they do not migrate above defined acceptable limits.
Minimising migration in Inks
Low migration inks are mainly recommended when it comes to UV/EB and conventional sheetfed inks especially if thin film substrates or paper material with weak barrier properties are used for primary packaging. Low migration UV curing inks are based on specialty raw materials like high molecular weight oligomers and polymers, together with polymeric photoinitiators, which are multi-functional and non-migrating. Fast curing ink recipes are generally 100% solids and aim to get high cross-link density.
UV inkjet fits with narrow web printing on relatively thick material such as labels and direct-to-shape. Inkjet printing, however, may have some room for improvement. Its disadvantage is that it uses low viscosity inks containing low molecular weight compounds that can pass through substrates more easily than the relatively heavyweight ingredients of offset and flexo inks.
To meet UV and EB curing needs for food packaging and labels, proper curing is absolutely critical. Partly dried or cured ink greatly increases the risk of migration and can lead to organoleptic changes in the packaged goods. Few post-cure chemical fragments left behind by UV and EB inks tend to be “functionally reactive,” which makes them non-migrating. Curing efficiency is everything in packaging printing with inks made for UV and EB exposure. Only with a 100% cure will ink components be fully cross-linked within a layer from which they cannot migrate.
EB curable inks are one of the best options for packaging because they do not contain photoinitiators, which are potentially migratable in elements in UV inks, as the energy provided by EB irradiation is sufficient to initiate curing.
Flexo/gravure have an advantage since their evaporative inks leave little or no migratable residue behind.
Birla Carbon Specialty Blacks
We have a wide range of specialty blacks with high chemical purity, superior flow with varying jetness requirements, meeting strict food contact regulations needed by the EU-food & skin contact, US-FDA, Swiss Ordinance, JHOSPA recommendations, the Chinese legislation and others.
We offer several carbon blacks under the Raven and Conductex brand names which are recommended for food packaging inks and coatings, suitable for indirect food contact.
Glossary :
- EuPIA : European Printing Ink Association
- EU : European Union
- EB : Electron Beam
- UV : Ultra Violet
- GMP : Good Manufacturing Practice
- JHOSPA : Japan Hygienic Olefin and Styrene Plastics Association
- FDA : Food and Drug Administration
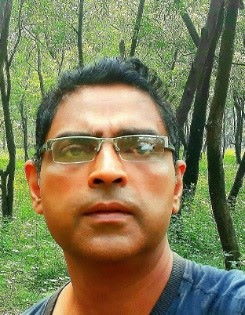
CHINMOY DHOLE
Chinmoy Dhole is a New Product Development Manager for the specialty blacks business at Birla Carbon in Asia. He leads development for new carbon blacks made in Asian plants and drives the execution and field initiatives related to strategic growth projects in Asia. Chinmoy has over 15 years of carbon black industry experience in a variety of specialty applications like Inks, Coating, and Plastics.
Chinmoy joined Birla Carbon in 2010. He holds a Master’s degree in Polymer from the Indian Institute of Technology (IIT), Kharagpur.
WANT TO LEARN MORE ABOUT CARBON BLACK AND THE PROPERTIES THAT MAKE IT IDEAL FOR YOUR PLASTICS, COATINGS, AND INKS APPLICATIONS?
Leave A Comment