BIRLA CARBON BLOG
INSIDER KNOWLEDGE FOR ALL THINGS CARBON BLACK
The Evolution of Anti-Vibration Systems in Automotive Applications – Part 2
Reading Time: 3.0 minutes
As discussed in Part 1 of this article, the development of elastomeric anti-vibration systems (AVS) in automotive applications plays a crucial role in improving the overall driving experience. These systems rely on the properties of elastomer composites to provide effective vibration isolation and overall noise, vibration, and harshness (NVH) reduction. Part 2 of this article will focus on the specific challenges posed by the transition to electric vehicles and how these elastomeric components are being integrated into electric vehicle architectures.
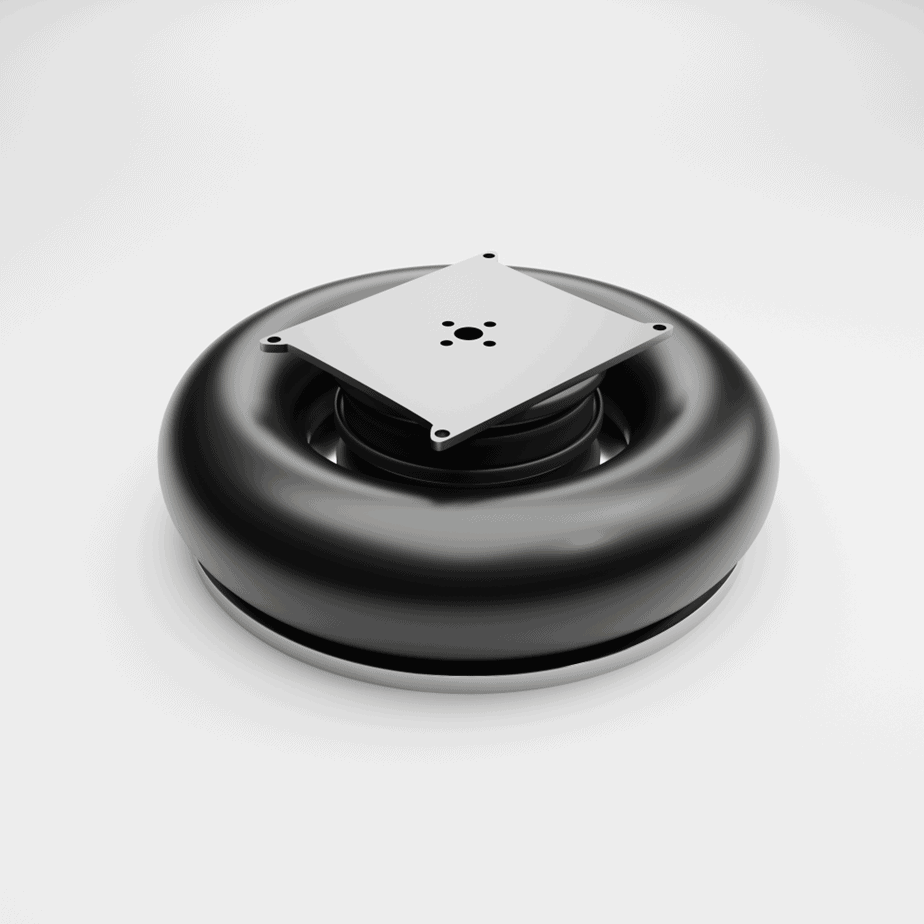
Challenges in AVS for Electric Vehicles
The transition to electric vehicles (EVs) and hybrid electric vehicles (HEVs) has brought new challenges to the design and implementation of AVS. The differences in the performance requirements and applications of elastomeric components between traditional internal combustion engine vehicles and EVs need to be understood and addressed.
Different Vibration Sources
EVs have different vibration sources, such as electric motor and drivetrain vibrations, which differ in frequency and amplitude from those generated by internal combustion engines. This requires different elastomeric materials and designs for effective vibration isolation and control often by tuning the natural frequency.
Weight Reduction and Noise Reduction
Weight reduction is a critical aspect of EV design, as it directly impacts the vehicle’s range and efficiency. Consequently, there is a need for lightweight elastomeric materials and components that can still provide effective vibration and noise reduction. At the same time, EVs are inherently quieter than their combustion engine counterparts, which means that road and suspension noise become more noticeable, further emphasizing the need for effective NVH reduction.
Integration of Elastomeric Components in EV Architectures
Adapting AVS to EV architectures requires a thorough understanding of the specific requirements and challenges posed by EVs. Manufacturers must consider the unique vibration sources, weight reduction needs, and thermal management concerns when designing elastomeric components for EV applications.
Customized Elastomeric Solutions
To meet the specific needs of EV manufacturers, elastomeric component suppliers must develop customized solutions that address the unique requirements of EVs. This may involve the development of new materials, designs, or manufacturing processes to create components that provide effective vibration isolation and control in EV applications.
Modeling and Simulation Tools
Advanced modeling and simulation tools play a crucial role in the development of elastomeric components for EVs. These tools allow manufacturers to predict the performance of their designs under various operating conditions and to optimize the components for maximum effectiveness and efficiency. This is especially critical as automotive companies push towards virtual product development which eliminates physical prototypes and testing in the development process.
Active and Adaptive Elastomeric Components
The development of active and adaptive elastomeric components, such as electrically activated mounts and adaptive hydraulic suspension bushes, represents another significant advancement in AVS technology. These components can adjust their properties and performance in real-time, allowing for optimal vibration isolation and control under varying driving conditions.
Collaborative Development
The evolution of the automotive industry towards EVs requires a collaborative approach to the development of AVS. Manufacturers, suppliers, and researchers must work together to understand the unique challenges posed by EVs and to develop innovative elastomeric materials and components that can meet these demands.
Conclusion
As the automotive industry continues to transition towards EVs, the role of elastomers in AVS will become even more critical, with new challenges to overcome and opportunities to innovate. By understanding the specific requirements of EVs and developing advanced elastomeric materials and components, manufacturers can continue to improve the overall driving experience and NVH performance in the vehicles of the future.
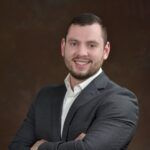
James Kollar
James Kollar is a scientist in the Birla Carbon rubber product development group. His work includes developing and evaluating new carbon blacks and synergistic materials for rubber applications. James joined Birla Carbon in 2018 and holds a master’s degree in chemistry. He is interested in reinforcing material networks and network formation mechanisms within polymer systems.
WANT TO LEARN MORE ABOUT CARBON BLACK AND THE PROPERTIES THAT MAKE IT IDEAL FOR YOUR PLASTICS, COATINGS, AND INKS APPLICATIONS?
Leave A Comment