BIRLA CARBON BLOG
INSIDER KNOWLEDGE FOR ALL THINGS CARBON BLACK
Maximizing Curing of UV Inks and Coatings with Carbon Black
12 / 01 / 2020 by Robert Fisher

Reading Time: 3.25 minutes
UV-curable inks and coatings are a high growth market for various industries such a printing ink, particularly for food packaging, floor coatings, and 3D printing. These materials offer high gloss, low/zero VOC (volatile organic compound), and many other advantages compared to other liquid chemistries. Such systems commonly use carbon black for pigmentation, although the very properties that allow carbon black to offer high color strength and gloss also bring some unique challenges since this can reduce the curing response of the formulation. Poor cure can lead to diminished physical properties and reduced production/printing rates. Despite this, there are several steps that a formulator can take which will allow a highly pigmented system to still offer effective curing performance and not require slower line speeds or investment in additional curing equipment.
Surface Area Considerations
One of the easiest ways to improve the cure response of a UV system is to use a carbon black with a reduced surface area to minimize UV absorption by the pigment. One must take care however to not use too low a surface area that will result in an unacceptable loss in color performance. Using a carbon black with a reduced structure (OAN) can also allow slightly higher tint strength and a bluer undertone, as well as reducing the viscosity of the system at equivalent surface areas. Birla Carbon’s Raven 1060 Ultra is one example of a product with a balance of color performance and through-cure, low structure, as well as a post-treatment. These allow for very good dispersion and rheology in UV formulations. For formulators who require a higher tinting strength than Raven® 1060 Ultra®, Raven® 1100 Ultra® is also an attractive option. In addition, Birla Carbon plans to introduce several new products for this application, as our business strategy is to have specific focus on the next generation products for UV inks by working closely in partnership with key players in the marketplace.
Photoinitator Selection
Another improvement in curing performance that can be introduced to a formulation containing a high loading of carbon black, or high surface area carbon blacks, is to optimize the photoinitator (PI) package. One of the most common photinitiators used in UV formulations is benzophenone due to its ease of use and low cost, however the UV absorption spectra for this particular PI is largely overlapped by the UV absorption for carbon black, which results in poor curing.
Alternative PIs that allow better curing response include phosphine oxides such as BAPO or thioxanthones such as ITX and DETX. One common mistake that novice formulators can make to increase cure response is simply increasing the PI loading. Although in some cases this can help, a common side effect is that while surface cure is acceptable, through-cure is actually reduced.
Crosslink Density
UV curable systems usually contain a blend of various monomers and oligomers to influence the dry films properties such as adhesion, scratch resistance, and cure speed. For heavily pigmented systems including those with carbon black, using higher functionality materials allows for a more reactive system to compensate for the decrease in UV radiation able to start the curing reaction.
Higher functional monomers and oligomers with 3 or more acrylate groups such as trimethylol propane triacrylate (TMPTA) can give a higher crosslink density without sacrificing viscosity. Care must be taken however to not make the dry film too brittle in the process.
For more information on how Birla Carbon can help you find the right carbon black for your UV chemistry, reach out to our technical team via the Contact Us page.
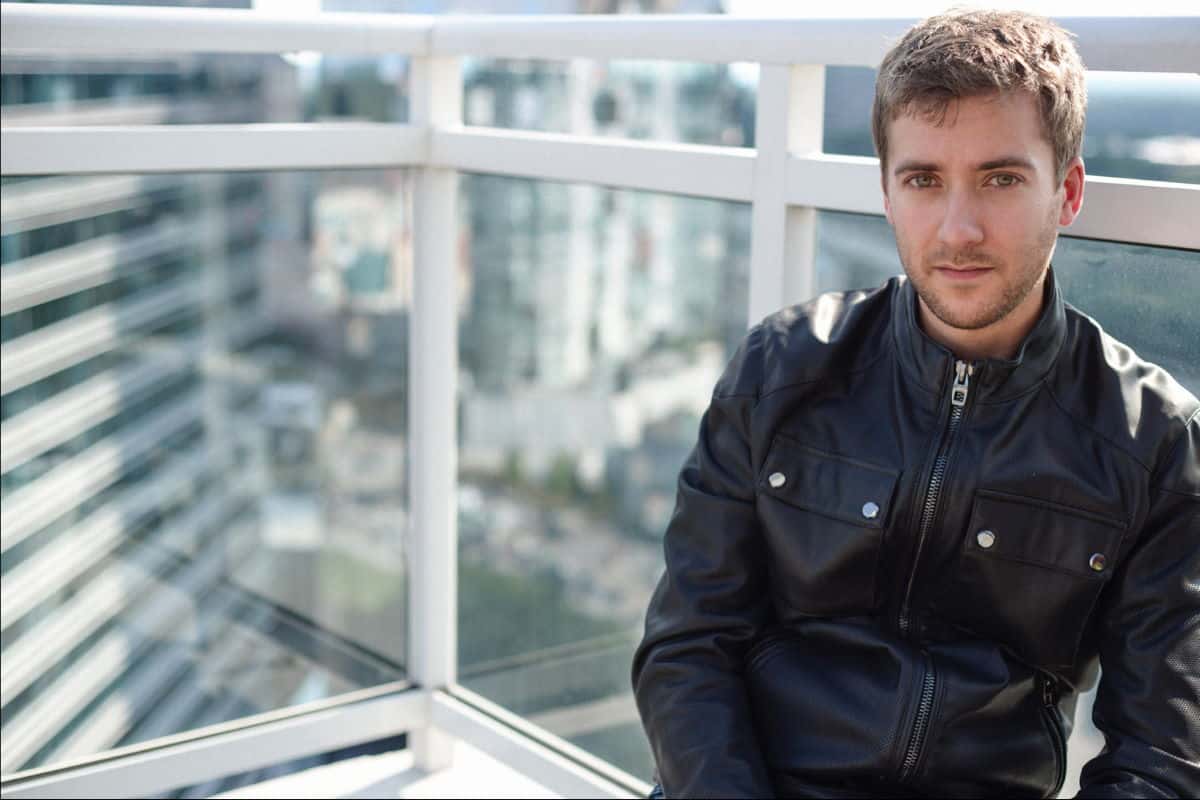
Robert Fisher is part of the technical Business Development team for Birla Carbon’s North American Specialty products. He is responsible for identifying and capturing new technical business opportunities while servicing and growing existing customers. Robert has a Master’s degree in Materials Science from Georgia Tech and a Bachelor’s in Polymer Science, also from Georgia Tech. He has a background in inks and coatings formulation in addition to energy storage applications. Robert currently lives in Atlanta, GA.
WANT TO LEARN MORE ABOUT CARBON BLACK AND THE PROPERTIES THAT MAKE IT IDEAL FOR YOUR PLASTICS, COATINGS, AND INKS APPLICATIONS?
Hello!
We are a trading company in South korea.
I’m Choi from GCO & Co.
My customer develops UV curable adhesive,
they want the UV adhesive to be black,
but it is difficult to harden to the bottom
because the adhesive’s thickness is 1mm, so UV is
blocked by black pigment.
If you have a solution for this, please let me know.
The customer is a South Korean electronics company.
It is a good opportunity.
Non conductive is even more better
Best regards,
Choi
Thank you for you comment, we will be reaching out to you for offering support